How hard is tungsten carbide?
The hardness range of tungsten carbide is generally 86-94HRA, which is equivalent to 69-82HRC. Different types of tungsten carbide have different hardnesses. For example, cobalt-based alloys and aluminum-based alloys have higher hardness, generally between HRA82-94.
The hardness of tungsten carbide can also maintain a high level at high temperatures. For example, at 900-1000°C, cemented carbide can still maintain high hardness and show excellent wear resistance. In addition, the hardness of wolfram carbide decreases with the change of temperature. For example, at 540°C, the hardness is 82-87HRA, and at 760°C, the hardness can still maintain 77-85HRA.
In order to let everyone better understand the performance of cemented carbide, I have selected cemented carbide YG10 grade for a detailed explanation. Tungsten carbide grade YG10 is equivalent to the international standard ISO K10.
Tungsten carbide YG10 has the characteristics of high hardness, high strength, wear resistance, corrosion resistance and high temperature performance. Its hardness reaches 86-90HRA, which is higher than most metal materials and is very suitable for manufacturing high-hardness and high-precision cutting tools. The chemical composition of YG10 includes carbon (C), cobalt (Co) and tungsten (W), specifically 0.8-1.2% carbon, 9.5-10.5% cobalt, and 89.2-89.8% tungsten1.
- Mechanical properties:
· Density: 14-14.5 g/cm³
· Hardness: HRA91-HRA92
· Bending strength: 3500 N/mm²
- Application areas:
YG10 wolfram carbide is widely used in the manufacture of cutting tools, punching and shearing tools, molds and mining machinery parts. Specific applications include:
Cutting tools: such as drills, reamers, blades, milling cutters, etc.
Punching and shearing tools: such as punching machine dies, punching machine dies, shear knives, etc.
Molds: such as injection molds, extrusion molds, die-casting molds, etc.
Mining machinery parts: such as mining machine blades, mine car hydraulic cylinder mandrels, etc.
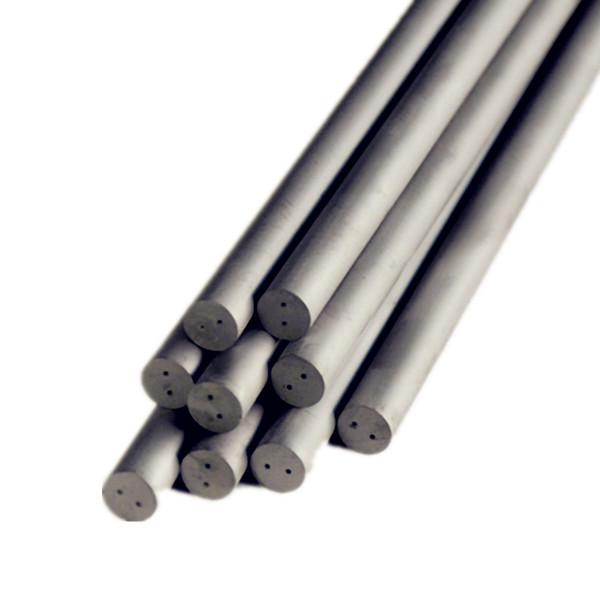
How hard is tungsten carbide?
- Preparation method:
First, select ultra-fine grain high-quality alloy powder, whose composition is mainly tungsten carbide (WC) and cobalt (Co) content is 10%. Then YG10 cemented carbide rods are manufactured by powder metallurgy sintering. This method involves mixing tungsten carbide and cobalt powders, and then sintering at high temperature and pressure of 1300℃ to 1500℃ to form cemented carbide materials with the desired shape and size. This process ensures the uniformity and high performance of the material.
Problems and solutions that may be encountered during the preparation process:
During the preparation process, problems such as large brittleness of the material and inability to prepare large-sized or complex-shaped products may be encountered. In order to solve these problems, a partial instantaneous liquid phase connection method can be used, using a Ti/Ni/Ti layer as an intermediate layer to prepare the joint through partial instantaneous liquid phase connection. This method can improve the toughness and application range of the material to a certain extent.