How to make cemented carbide
The production process of cemented carbide is a comprehensive and complex manufacturing process, which requires material preparation, powder mixing, molding, sintering, post-processing and other links. The following will introduce the production process of cemented carbide and the process operation of each link in detail.
1. Material preparation:
The main materials for the production of cemented carbide are tungsten powder, cobalt powder and carbide powder. Tungsten powder, as the main component of cemented carbide, has the advantages of high hardness and high density; cobalt powder, as a bonding phase, plays a role in enhancing the toughness and ductility of the alloy; carbide powder is another main component in cemented carbide, which improves the hardness and wear resistance of the alloy. In the material preparation stage, various raw materials need to be prepared according to the requirements of the alloy formula, and their quality and proportion must be strictly controlled. Among them, the particle size, purity, shape and other parameters of tungsten powder and cobalt powder have an important influence on the performance of cemented carbide, and need to be precisely screened and selected.
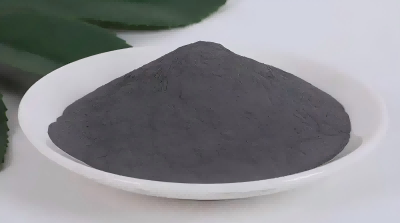
2. Powder mixing:
It is a key link in the preparation of cemented carbide to mix tungsten powder, cobalt powder and carbide powder evenly according to a certain formula ratio. Through powder mixing, various raw materials can be fully mixed to ensure that the composition of the final alloy is uniform. The powder mixing process usually adopts mechanical mixing, that is, the raw materials are placed in a ball mill and other equipment for dry mixing or wet mixing. During the mixing process, it is necessary to control parameters such as mixing time, speed and temperature to ensure that the mixing effect reaches the best state.
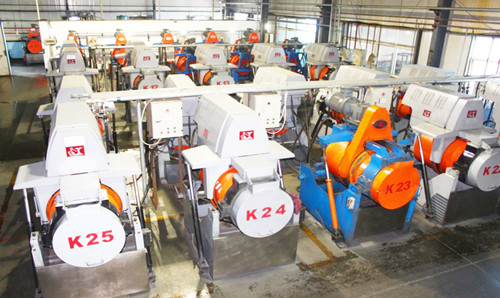
3. Forming:
The forming process of cemented carbide mainly includes two steps: pressing and forming. Pressing is to press the mixed powder through a mold to form a dense blank. Forming is to make the final shape of the alloy through a mold, which can be different shapes such as cemented carbide plates, cemented carbide round bars, carbide cylinders, etc. In the forming process of cemented carbide, it is necessary to consider the control of parameters such as pressure, temperature, and speed to ensure the forming quality of the alloy. In addition, the blank after forming needs to be annealed to eliminate the stress generated during the forming process and improve the yield and density of the alloy.
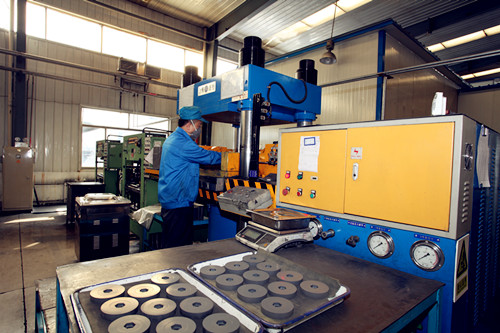
4. Sintering:
Sintering is the core process link of cemented carbide production. Through high-temperature sintering, elements such as tungsten, cobalt, and carbon react to form a strong binding phase to achieve the hardness and wear resistance of cemented carbide. The sintering temperature is generally between 1300℃ and 1600℃, and the sintering time and atmosphere also affect the performance of the alloy. During the sintering process, the alloy also needs to be cooled, annealed and other treatments to improve the stability and wear resistance of the alloy. At the same time, the sintering furnace needs to be periodically inspected and maintained to ensure the stability and controllability of the sintering process.
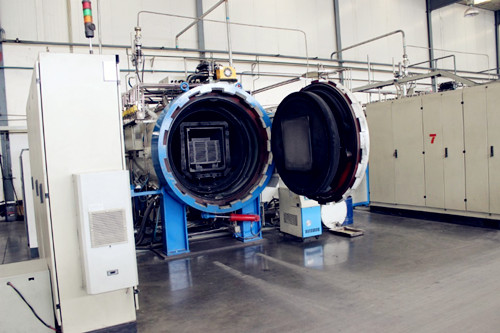
5. Post-processing:
After the production of cemented carbide is completed, post-processing processes are required, including polishing, cleaning, and testing. Polishing is to improve the surface finish and precision of the alloy; cleaning is to remove surface dirt and impurities to ensure the service life and performance of the alloy; testing is to test the physical properties and chemical composition of the alloy to ensure the stability of the product quality.
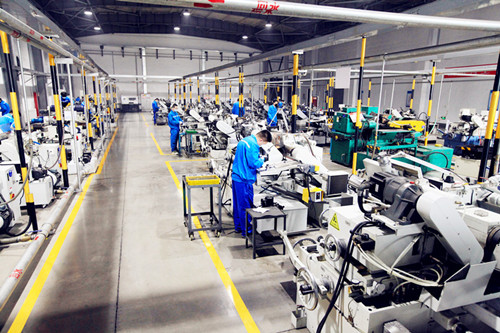
In addition, cemented carbide also needs to undergo subsequent processing procedures such as cutting, engraving, and packaging to finally form a finished product. In the post-processing process, attention should be paid to environmental protection and energy saving, and reasonable process flow and equipment should be adopted to reduce energy consumption and waste emissions. In general, the production process of cemented carbide is a meticulous and tedious process, which requires close cooperation of all links, reasonable process flow, accurate process parameters, and stable equipment operation, in order to produce cemented carbide products with stable quality and excellent performance. I hope that the above text can help you understand the production process of cemented carbide.