How to machine tungsten carbide
Cemented carbide materials are made of metal powder tungsten carbide powder and solid binders such as bonding metals such as cobalt, iron, nickel, etc. through pressing, sintering and other processes. They have high hardness (hardness range 86HRA-94HRA), high strength, high wear resistance and other excellent properties, so they are difficult to be processed by conventional cutting tools. How to machine tungsten carbide ? I will explain the cutting of cemented carbide and the cutting methods of cemented carbide bars and plates in detail through the following content.
I. Traditional cutting methods for cutting tungsten carbide and cemented carbide
Traditional cemented carbide cutting methods include grinding, electric spark, wire cutting and other methods, which are briefly introduced below.
1. Grinding method.
Grinding method is a commonly used cemented carbide cutting method, which can be cut using CBN grinding wheel, green silicon carbide grinding wheel and diamond grinding wheel. According to the toughness, hardness and wear resistance of cemented carbide, selecting appropriate cutting parameters and tools for grinding can obtain satisfactory cutting results. However, this method is suitable for small area cutting, and long-term grinding can easily lead to tool wear and low processing efficiency.
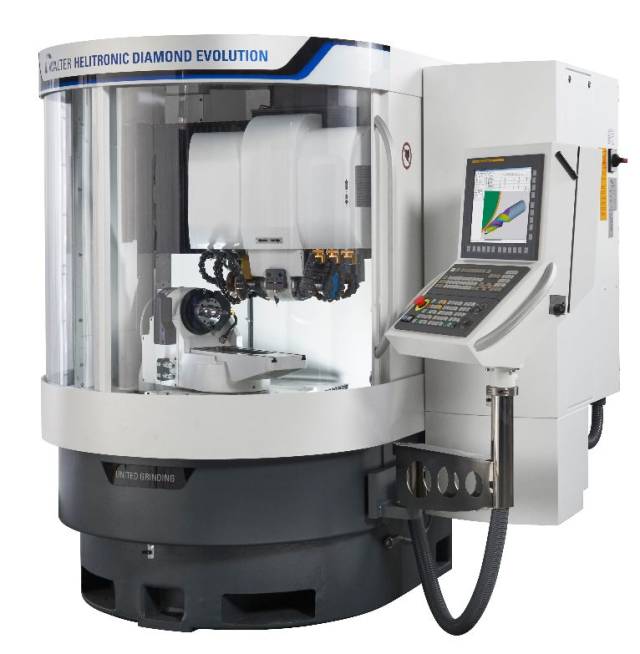
2. Electrospark machining of tungsten carbide.
Electrospark machining, also known as discharge machining or electro-erosion machining, uses the electro-corrosion phenomenon of pulse discharge between the tool electrode and the workpiece to erode excess metal to achieve the predetermined machining requirements for part size, shape and surface quality. This technology has the characteristics of non-contact machining and can achieve complex shapes and precision dimensions on high-hardness, high-brittleness, and difficult-to-machine materials.
(1). High-precision machining: Electrospark machining can achieve micron-level or even nano-level machining accuracy, meeting the high-precision requirements of cemented carbide parts.
(2). High surface quality: During the electrospark machining process, there is no direct contact between the tool electrode and the workpiece, avoiding the damage of the cutting force to the workpiece surface, so that a higher surface quality can be obtained.
(3). Complex shape machining: Electrospark machining is not limited by the hardness and brittleness of the material, and can process cemented carbide parts of various complex shapes and structures.
Although electrospark machining has many advantages in cemented carbide machining, it also has some limitations and challenges. First, the electrospark machining speed is relatively slow and the machining efficiency is low. Secondly, a large amount of electric energy and electrode materials are consumed during the EDM process, which is costly. In addition, EDM requires high equipment accuracy and stability, and is difficult to operate and maintain. This is commonly used for machine tungsten carbide blocks, EDM blocks for mould industry. And also cut tungsten carbide rods.
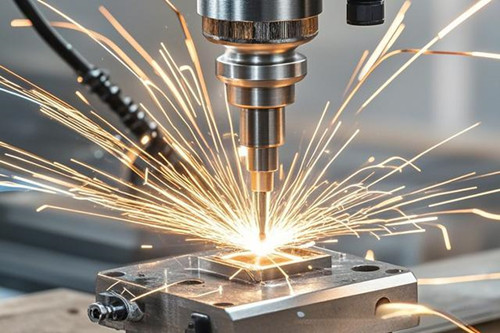
3. Wire cutting method for processing cemented carbide and tungsten carbide.
Wire cutting is a high-speed cutting technology. The electric spark generated by high-frequency current causes the linear cutting wire to enter the workpiece in a serrated manner and form tiny etchings on the surface of the workpiece. As the wire serrations are continuously removed, large-area cutting can be achieved. However, wire cutting has certain limitations. For example, the thickness, shape and size of the workpiece need to be within a certain range. As a conductor, cemented carbide can meet the requirements of wire cutting. According to the running speed of the electrode wire, EDM wire cutting machines are mainly divided into two categories: high-speed wire EDM wire cutting machines and low-speed wire EDM wire cutting machines. The former electrode wire (molybdenum wire) reciprocates at a high speed of 8-10m/s, and the processing speed is fast, but the electrode wire is easy to shake, which affects the processing quality; the latter electrode wire (copper wire) moves unidirectionally at a speed lower than 0.2m/s. The electrode wire is no longer used after discharge, and the work is more stable, the processing quality is better, but the processing speed is relatively slow. Compared with processing other mold materials, the processing productivity of cemented carbide on CNC wire cutting machine tools is the lowest. For thinner workpieces with a thickness of less than 20mm, wire cutting is relatively easy, and the surface quality and processing speed are ideal. For thicker workpieces with a thickness of more than 20mm, the processing difficulty increases, and wire breakage and unstable processing are prone to occur. Solutions include replacing thicker electrode wires, using more stable working fluids, and adjusting machine tool parameters. The maximum length of cemented carbide wire cutting can reach 600mm. Cemented carbide performs particularly well in slow wire cutting. Slow wire cutting has high processing accuracy and good surface quality, and is particularly suitable for processing cemented carbide parts with complex shapes and high precision requirements. Due to the high hardness and good wear resistance of cemented carbide materials, slow wire cutting can effectively avoid the loss of electrode wire, thereby extending the service life of electrode wire and improving processing efficiency. A lot of factories use this method to cut tungsten carbide rod.
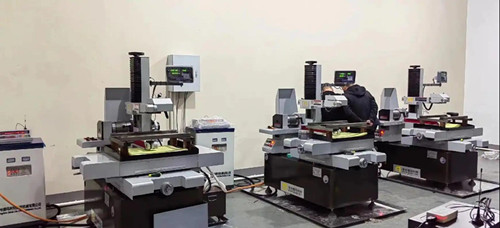
II. Laser cutting method for machine wolfram carbide and cemented carbide
Laser cutting is a new type of cemented carbide cutting method that has emerged and developed rapidly in recent years, with the advantages of high efficiency, high precision and automation. When cutting cemented carbide, laser cutting can make the incision width less than 0.2mm, the cutting speed is fast, and it has obvious advantages in cutting quality and efficiency.
However, there are also some problems with laser cutting. For example, the high temperature generated during the cutting process can easily cause material deformation, damage and defects. At the same time, the price of laser cutting equipment is relatively high and is not suitable for mass production.
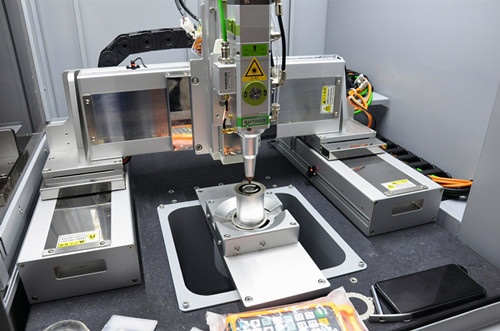
III. Ultrasonic cutting method for processing tungsten carbide and cemented carbide.
Ultrasonic processing is processed by high-frequency vibration, and its frequency is usually above 20kHz. During the processing process, the sound waves generated by ultrasound make the processing tool vibrate at an extremely high speed, thereby producing high-speed cutting, friction, grinding and loss at the microscopic level to achieve the processing of the workpiece. Ultrasonic machining is widely used in the cutting of cemented carbide materials because of its high efficiency, high precision, high surface finish and suitability for difficult-to-process materials.
Principles and advantages of ultrasonic cutting of cemented carbide:
Ultrasonic machining cuts through high-frequency vibration and has the following advantages:
High efficiency: Ultrasonic vibration is high-speed and has a small action area, so the workpiece can be processed in a very short time.
High precision: Since the vibration is very small, a very high processing accuracy can be obtained.
High surface finish: The small action area makes the surface finish high, reducing the subsequent processing steps.
Applicable to difficult-to-process materials: Since ultrasonic machining does not require a large amount of heat to be generated, difficult-to-process materials can be processed in a relatively short time.
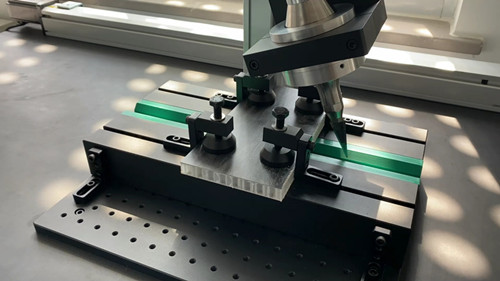
IV. Summary
How to machine tungsten carbide ? Different cemented carbide cutting methods have their advantages and disadvantages and scope of application. Traditional cutting methods are suitable for small-area cutting and small-batch processing, while laser cutting methods are more suitable for large-area cutting, high-efficiency and high-precision processing. Therefore, it is crucial to choose the right cutting method according to different processing requirements and material properties.